Recent Posts
-
2025.06.25
エーディコアとロサンゼルスの思い出
-
2025.05.30
ビジネスマナーとブランド力
-
2025.04.30
ブランドを支えるもの
-
2025.03.27
思わぬ場所で出会うエーディコアの家具
-
2025.02.27
来日公演大盛況、マルーン5・ジェームズさんお宅訪問記
-
2025.01.31
六本木ショールームのイルミネーションシステム
-
2024.12.25
独立系時計ブランドとエーディコア
-
2024.11.29
2025モデル撮影と新ショールームでの新作展示会
-
2024.10.30
東京ショールームが移転いたします
-
2024.09.30
椅子やソファの印象を決定づけるファブリック
Back Number
2025年
2024年
2023年
2022年
2021年
2020年
2019年
2018年
2017年
2016年
2015年
2014年
2013年
2012年
2025.6.25 DESIGN
エーディコアとロサンゼルスの思い出
AD CORE DEVISE DESIGN BLOG Vol.158
エーディコア・ディバイズのアイコンとも言える代表作の CERVO AD-861 が誕生したのが1985年。それから様々な時代を経て40年が経過しました。おかげさまで CERVO は現在もご注文をいただくロングセラー商品です。開発当時は、日本の美意識を意識しつつもイタリアのモダンデザインに少しでも追いつこうと、当時としては画期的な構造でエッジの効いたデザインでしたが、40年を経た現在では流行を何度か廻って、ちょっとヴィンテージの雰囲気も醸し出すアイテムになってきました。そろそろ「マスターピース」と呼ばれても良いのかな、なんて思える CERVO ですが、そんな CERVO との付き合いも30年になろうとしています。
「今までにないファニチャーブランドを創る」という理念からスタートしたエーディコア。当時の家具生産の常識からは逸脱した受注生産システムで、お客様が必要とする製品だけをご希望の仕様でお届けするスタイルを 目指しました。時はバブル経済が始まろうとしていた頃、カフェバーブームにも乗りその時大ヒットしたのが CERVO です。成形合板と木製の脚を金属パーツを介して組み立てたこの椅子は、昔ながらの職人さんからは「こんなの椅子じゃない」と揶揄されたこともありますが、この CERVO が椅子のデザイン性を広げることが出来たのではないかと思います。その後も、不均等厚成形合板に突板を張った製品や、3次元成型合板の加工の可能性を広げるなど、新しい取り組みを続けてきました。困難な時期でも毎年必ず新製品を発表し、展示会を開催してきました。夜中に図面を書き上げて、そのまま工場に車で向かうなんてこともありました。今ではほとんどなくなりましたが、新作の試作制作も夜中まで工場に通い詰めて作り込んでいたものです。新作の試作制作といえば夜通し作業、夜な夜なディテールを職人さんと作り込んで製品の完成度を上げていきました。そして、家具開発と同じくらいこだわりを持っていたのが製品カタログです。ブランド発足当初から、カメラマンの選定から製品の見せ方、カタログの形状から用紙、印刷の方法までオリジナルなモノを目指してきました。その中でも最もこだわってきたのが撮影のロケーションです。
撮影には製品を見せるためのスタジオ撮影と、イメージや世界観を表現するロケーション撮影があります。ロケ撮影はハウススタジオのレンタルが一般的ですが、当社では撮影に使われたことがないロケーションを探して撮影をしてきました。しかし、そんな物件探しも困難になって行き詰ってしまいました。そんな時、持ち上がったのがロサンゼルスでの撮影です。海外撮影なんて夢のようなことでしたが、いろんな出会いもあって、2007年からLA撮影をスタートしました。それまで、いろんな面でヨーロッパ志向だった私と瀬戸ですが、ロケハンで初めて訪れたロサンゼルスに衝撃を受けました。全てが自由でダイナミック、スケールの大きさに圧倒されました。ケーススタディハウスのコーニング邸から見た真っ青な空とダウンタウンの景色は今でも忘れられません。しかし海外撮影は想像以上に困難続き。初めての撮影の時でしたが、LAの倉庫に着荷した製品を確認しに行くと梱包の箱が潰れてぐしゃぐしゃに置かれていました。その時は瀬戸と2人で現地のフォークリフトを運転し、荷物を整理して全て梱包をし直しました。通関の問題で製品を引取ることが出来なかった時もあり、その時は「撮影キャンセルか・・・」と諦めかけた撮影前日の20時過ぎ、ギリギリで製品が引取れた時には皆で抱き合って大喜びしました。撮影でお借りする邸宅は住んでいるそのままの状態でお借りするので、撮影後はお借りする前より綺麗にしてお戻しします。搬出搬入を繰り返すので、普通の引越しよりも大変な作業になります。ライトJr 設計の住宅で撮影した時には(ライトの住宅はエントランスが狭いことで有名ですが)脱出シェルターのように狭い階段を通過しないといけないので鬼のように大変な撮影になりました。撮影時に作業を手伝ってもらうスタッフは現地で手配するのですが、ほぼ南米の出身者。お互い言葉が通じないどうしで身振り手振りを交えながらの楽しい共同作業でした。それ以外でも、数え切れないさまざまなトラブルがありましたが、それも今となっては良い思い出です。2007年から始まったLA撮影ですが、新型コロナウイルス感染の影響からコーディネーターのYasukoさんがロサンゼルスから日本に戻られたこともあり、2019年で一旦区切りをつけましたが、ロサンゼルスで撮影したたくさんの撮影画像はエーディコア・ディバイズの貴重な財産になりました。
2012年からスタートしたエーディコア・ディバイズのコラム。皆様に拙い文章をお送りしてまいりましたが、この6月をもって定年退職することになりました。毎回ネタ探しで苦労しながらもなんとか続けることができました。今まで読んでいただいた皆様、ありがとうございました。これからも独自の視点から家具の提案をお届けするブランド、エーディコア・ディバイズを引き続きよろしくお願いします。(開発 武田伸郎)
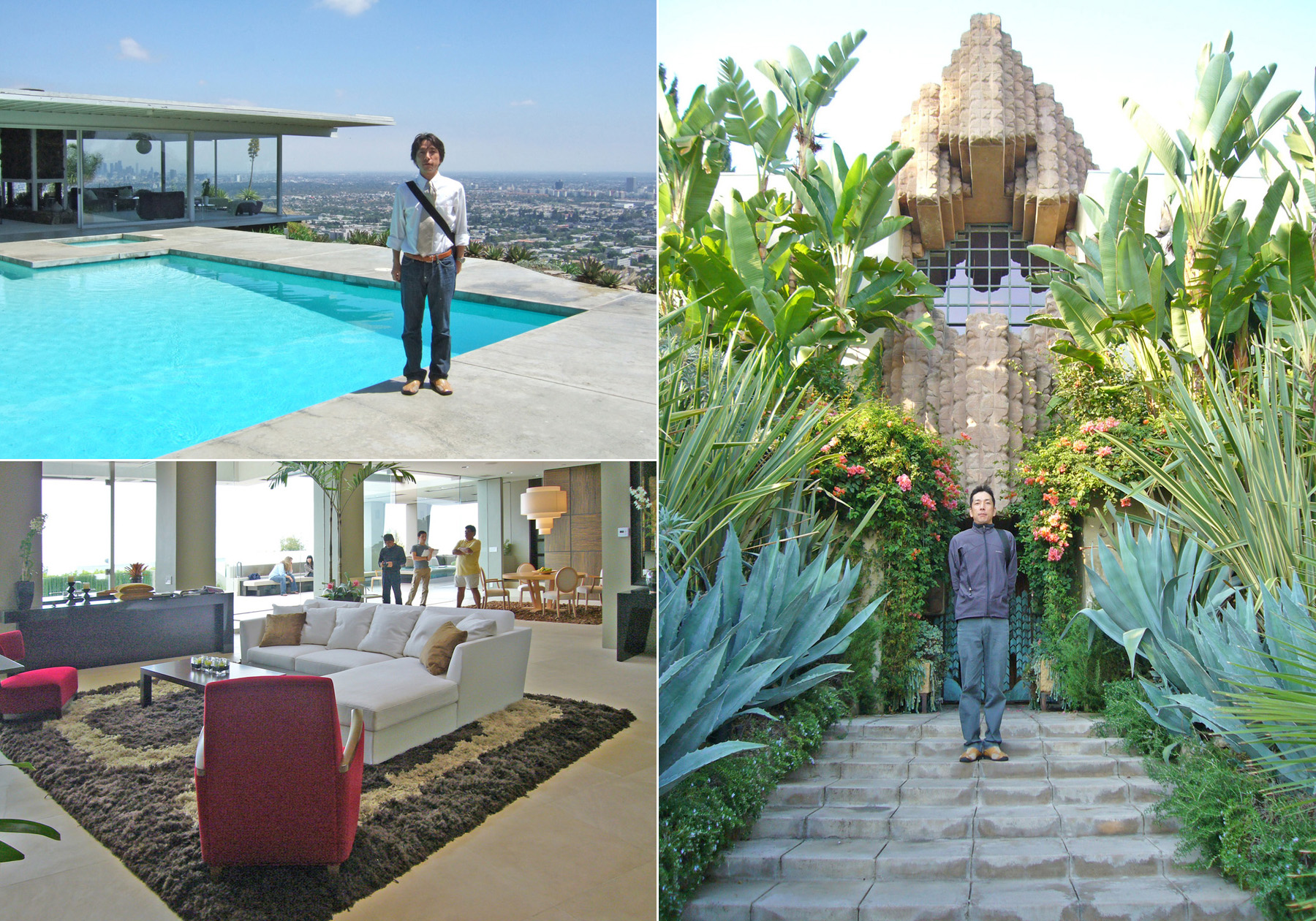
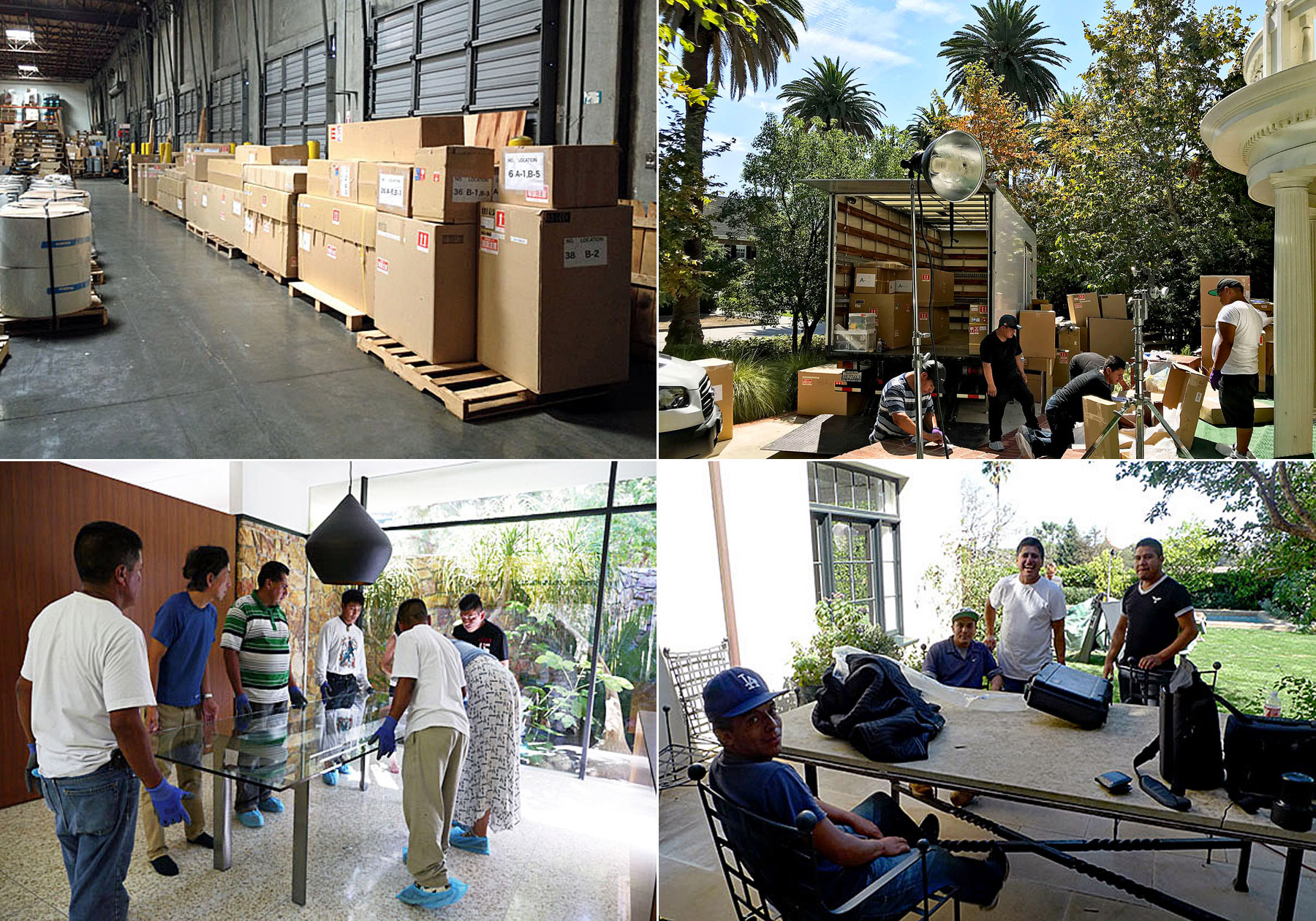
2025.5.30 DESIGN
ビジネスマナーとブランド力
AD CORE DEVISE DESIGN BLOG Vol.157
前回のコラムでお伝えしましたが、今年の4月よりエーディコア・ディバイズ東京本社に新しいスタッフが2名入社しました。2人のうち1人は新卒者、当社としては暫くぶりの社会人1年生を採用することになりました。大企業や上場会社では新入社員へむけて社会人としての心構えや基本的なマナーを身につけるため手厚い研修が実施されるようですが、中小企業では十分な時間をかけて研修を実施することは難しいのが現状です。当社でも採用のほとんどが中途採用の社会人経験者のため、新人研修は社内で出来る範囲で実施してきました。しかし今年は新卒者+全くの異業種からの転職ということもあり、アウトソーシングを活用したビジネスマナーの研修を受けてもらうことにしました。ビジネスマナーから社会人としての常識や仕事をする上での心構えまで、研修を受けたスタッフのレポートを見ると内容の充実ぶりが伺えます。そこで、当社では新人スタッフだけでなく、全社員が講師をお招きしてビジネスマナーの研修を受けることになりました。
新社会人に向けての(新社会人だけに限らないようですが)ビジネス・マナー講座の需要は益々高まっているようです。「社会人1年生でも当然身につけているであろう常識」が通用しなくなりつつある現在、専門部署があるような大企業であれば別ですが、中小企業の社内研修だけでビジネスマナーのスキルを習得させることは難しいようです。何かにつけ「ハラスメント」扱いされてしまう現代の状況では、社内のスタッフが社員に向けてマナー講習を行うよりも、客観的な立場でプロフェッショナルな方から教わる方がベストだと思われます。今回当社では、ANAビジネスソリューションの講師をお招きして研修を行いました。私自身、プロフェッショナルな方からビジネスマナー研修など受けたことがなく、長い間仕事に携わってきましたが正しいビジネスマナーの所作を理解していないこともたくさんあると思います。そんな「今さら聞けないビジネスの常識」も、こんな機会なら臆することなく聞くこともできます。名刺交換の作法から、お辞儀の仕方、挨拶や表情まで、なぜそうするのか、どうしてそのような作法が必要なのか分かりやすく実践しながらレクチャーしていただきました。大阪・名古屋のスタッフもZOOMミーティングで参加、研修の様子をモニターで見るだけでなく意見交換ができるようなセッティングで参加しました。講師の方から支社のスタッフに向けて質問を投げかけたり、支社のスタッフから意見を述べたり、ZOOMを活用することで全社で研修参加している感じも高まりました。
研修は3回を予定しており、先日2回目の講習を受けました。1回目はビジネスマナーの基本の「キ」。今までほとんど意識していなかったビジネス上の立ち居振舞いについて学ぶことができました。しかし、基本の「キ」が、なんと難しいことか。お辞儀の仕方や声の掛け方もさることながら、立っている姿勢や手先の収め方など、実際にやってみると本当に難しくて今まで出来ていなかったことを痛感しました。それから、身だしなみや立ち居振舞いがとても重要で、そのことが「相手」に対してたくさんの情報を伝えていることも教わりました。そういった一連の所作が相手に対する思いやりにつながり、信頼関係を築くことに繋がるのだそうです。そして2回目の研修は初回に学んだ基本をベースに、お客様の満足に向けたおもてなしについて。身だしなみから立ち居振舞い、会話力などを活かしてお客様と対応する際にどうしたらより満足いただけるのか?ショールームの中で実際にロールプレイングを行いながら研修を受けました。当社のスタッフ同士で行う接客マナーのロールプレイングは、気恥ずかしさも吹き飛ばして真剣に実践し、研修時間を超えてしまうほどいろんな質問が出て活発な意見交換もあり初回よりさらに有意義な研修になりました。
いつの間にか身についてしまった所作や立ち居振舞いを変えていくことは大変なことですが、今回受講した研修で自分がどんな動きや対応をしているのか「気付き」の機会になりました。そして日頃の対応からお客差の満足度を上げていくためには、マニュアルを守るだけでは達成できず、個々の感性を磨きそれぞれの対応力を高めることが必要なのだと感じました。よく耳にする「ブランド力」とは、製品のクオリティーやデザイン性の高さだけに限らず、スタッフの立ち居振舞いや対応力も大切なファクターになります。対応力が全体で高まってくることでブランド力も底上げされます。あと1回予定している研修会、どのような内容になるのかは当日のお楽しみですが「ブランド力」を高められるような良い研修に出来ればと思います。(開発 武田伸郎)
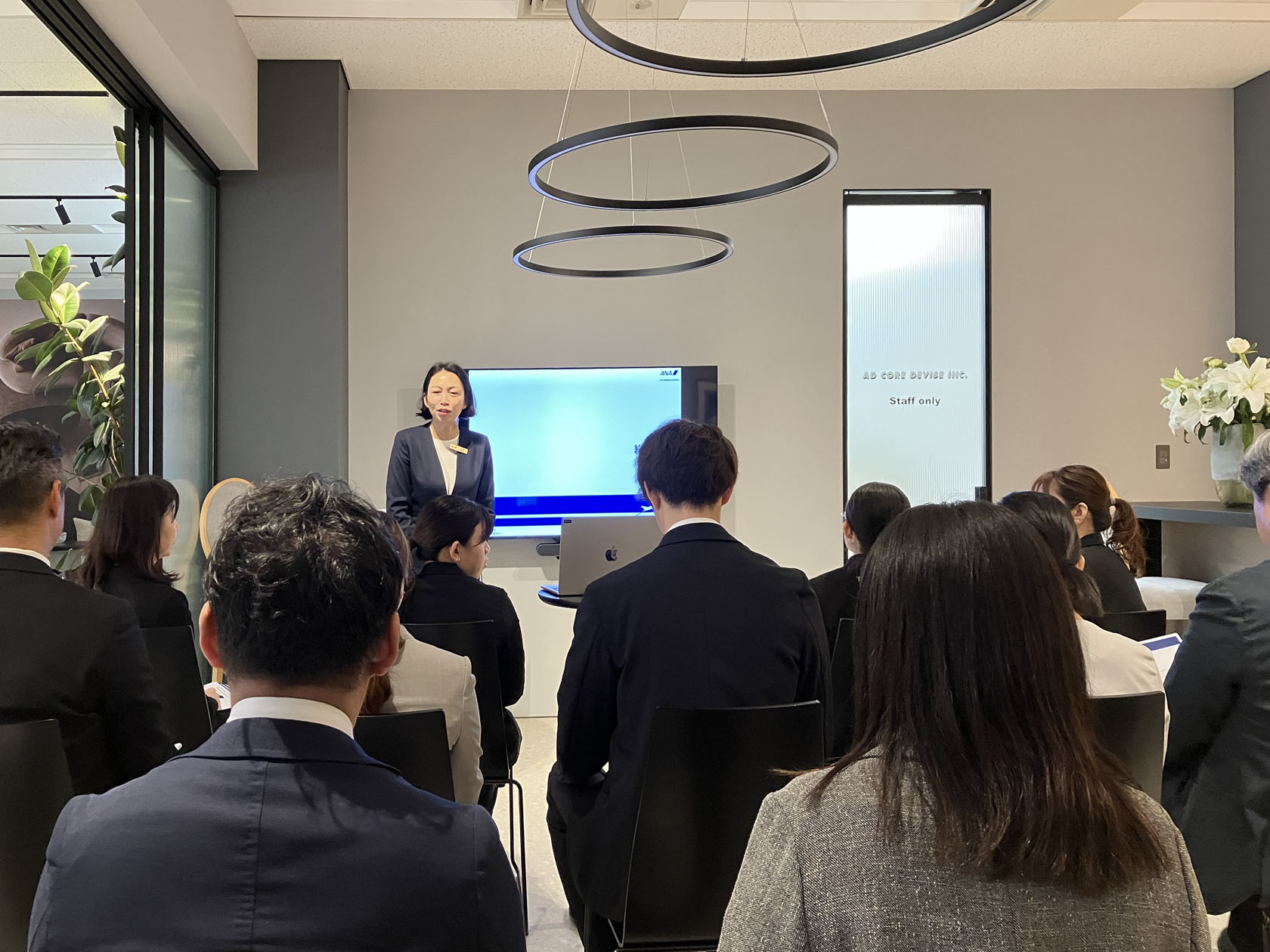
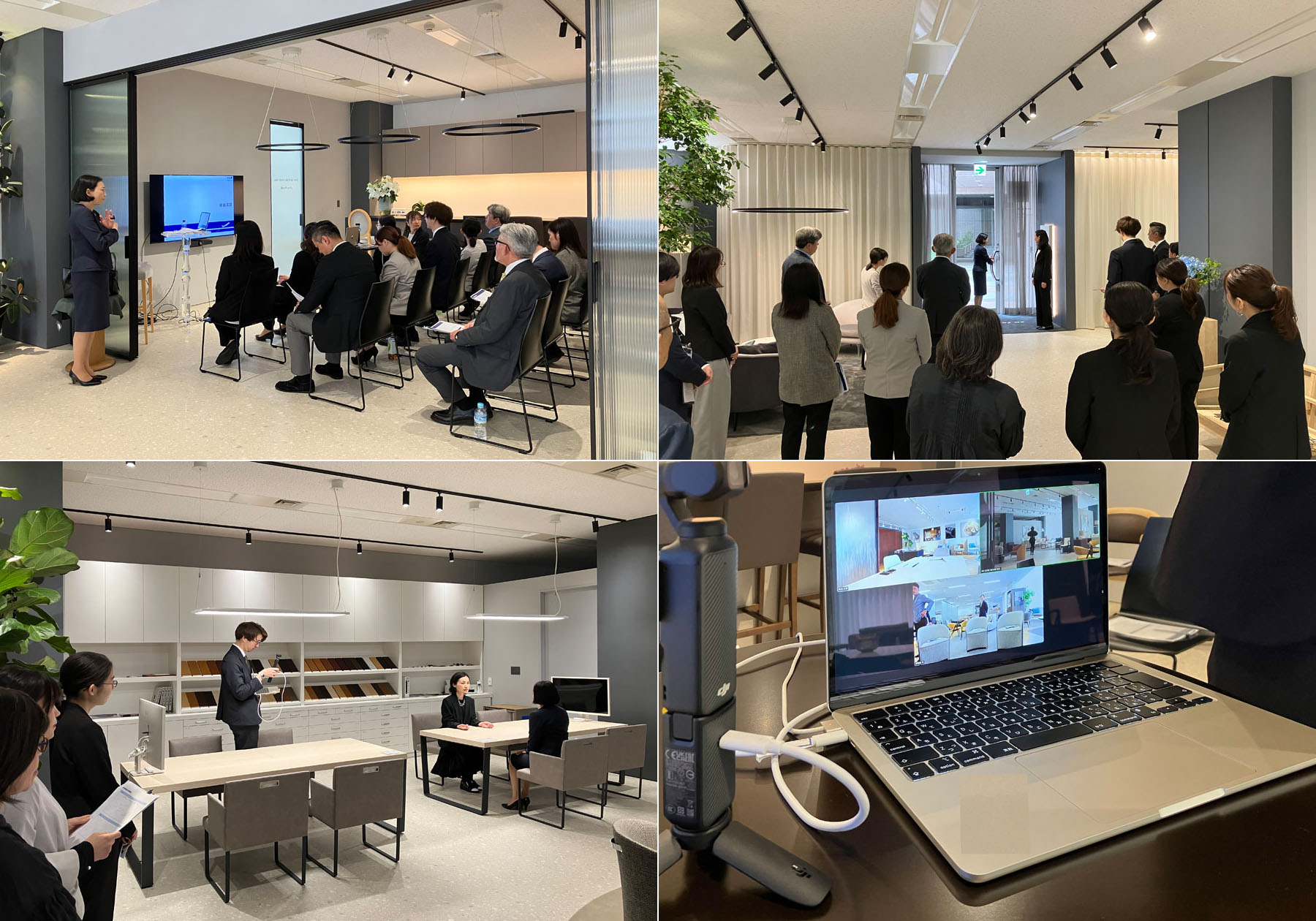
2025.4.30 DESIGN
ブランドを支えるもの
AD CORE DEVISE DESIGN BLOG Vol.156
日本では4月を新年度、学生から社会人まで新しい生活をスタートする節目の時期になります。新たな環境のもと、約一ヶ月が経過したわけですがGWを前に少し一息つく頃でしょうか。エーディコア・ディバイズでも4月より新しいスタッフが入社し、社会人としての基本的なスキルから業務的な事案まで日々研修を行いました。開発部として、家具の基本的な事から具体的な製品のディテールまで約2週間、研修を実施しました。家具メーカーのスタッフとして家具の知識を得ることは大切ですが、それと同じくらいエーディコアというブランドを理解することも大切です。今回の新人研修でエーディコアのブランドをレクチャーするにあたり「ブランド」の意味を改めて考える機会にもなりました。
1985年に小さな家具メーカーとして誕生したエーディコアがどのようにしてブランド力をつけ、どうやって維持してきたのか。今までの日本の「家具屋」の概念を覆したい、大量生産による低価格での販売競争には加わらない、必要なものを必要な分だけお客様の望む仕様でお届けする・・・当時ではありえないようなコンセプトを掲げ、現在までモノ作りを続けてきました。もちろん、製品の成り立ちやスペック、品質がブランド力を左右しますが、製品の背景にある思いやストーリーがブランドの魅力をさらに引き立てます。以前はブランドといえば、ファッションやジュエリーなどのハイエンドなモノをイメージしていましたが、現在はファストファッションの低コストのモノから野菜やお米のような食品までブランド力が必要とされているようです。かたや雲上ブランドの人気商品はお金を出しても手に入らない・・・そんなご時世で、最近は「ブランディング」の言葉にやや食傷気味な気分になりますが、先日、原宿で開催しているスペインの革製品ファッションブランド「LOEWE」のクラフテッド・ワールド展を見てきました。LOEWE(ロエベ)は150年以上前にスペインの革製品からスタートしたファッションブランド。スペイン王室御用達のブランドですが、現在はルイ・ヴィトンをはじめとするLVMHグループに属しています。この展示会を見るにあたっては「歴史ある革工房のブランドが、巨大資本のコングロマリットの傘下になり伝統的な技術やノウハウがいいように使われているんだろうな・・・」なんて、勝手なイメージを持って脚を運んだところがありました。ところが・・・(名前は伏せておきますが)これまで見てきた超有名メゾンのコンセプチャルな展示会とは比較にならないほど、とても素晴らしい展示会でした。
展示会全体に感じられたのが LOEWE(ロエベ)というブランドを「より良く理解して欲しい」というコンセプトでした。小さな革工房からスタートし、手作業の技術からモノ作りへのこだわり、素材を吟味する職人技と情熱。それが脈々と受け継がれ、コングロマリット傘下になったことでそのノウハウを新しいテクノロジーやシステムに取り込んでいる姿勢、そしてそれをストーリーとして見ることが出来る素晴らしい展示会でした。天然素材の中でも「革」は最もデリケートで見極めが難しい素材です。質感を活かすほど耐久性が損なわれ、耐久性を上げようとする程、素材本来の魅力が隠されてしまう。そんな扱い方が難しい素材を、昔ながらの経験と知識に基づいた職人技と最新技術によるオートメーション作業をバランスよく組み合わせ、モノ作りの工程をこんなに自然に受け継がれているのは初めて見たように思います。革カットの工程でも、オートメーション化されているのですがどこか優しい感じがするのは、常に人の目が行き届いているからでしょうか。革の耐久性を検査する試験体の色の美しさ、「クスッ」と笑ってしまうような試験機の動きなど、会場全体に笑顔になるような可愛い雰囲気がどことなく漂っていました。展示後半にはこれまでのファッションアーカイブのトルソーや、アート事業に携わるブランドとしての取り組みの紹介などで、展示会全体を統括していました。ハイエンドブランドが醸し出す、近寄りがたい美しさやカッコ良さとは違って、思わず微笑んでしまうような会場の雰囲気が僕にはとても心地よく感じた展示会でした。
どんなビジネスでも現代では「ブランド力」は必要不可欠です。でもそれぞれのブランディングの方法は様々。以前コラムでご紹介した独立系時計ブランド「ORIS」のように我が道を行くブランドもあれば、 LOEWEのように長い歴史を持ったブランドがコングロマリッドグループに参画して新たな発展を遂げるブランドもあります。いずれにしても大切なのは、ブランドの核となるものは守りつつ、時代の波に調和していく柔軟性ではないでしょうか。国産の独立系家具ブランドとして皆様にご愛顧いただいてきたエーディコア。これからも他とはちょっと違った視点でインテリアや家具の提案ができるブランドとして歴史を刻んでいければと思います。(開発 武田伸郎)
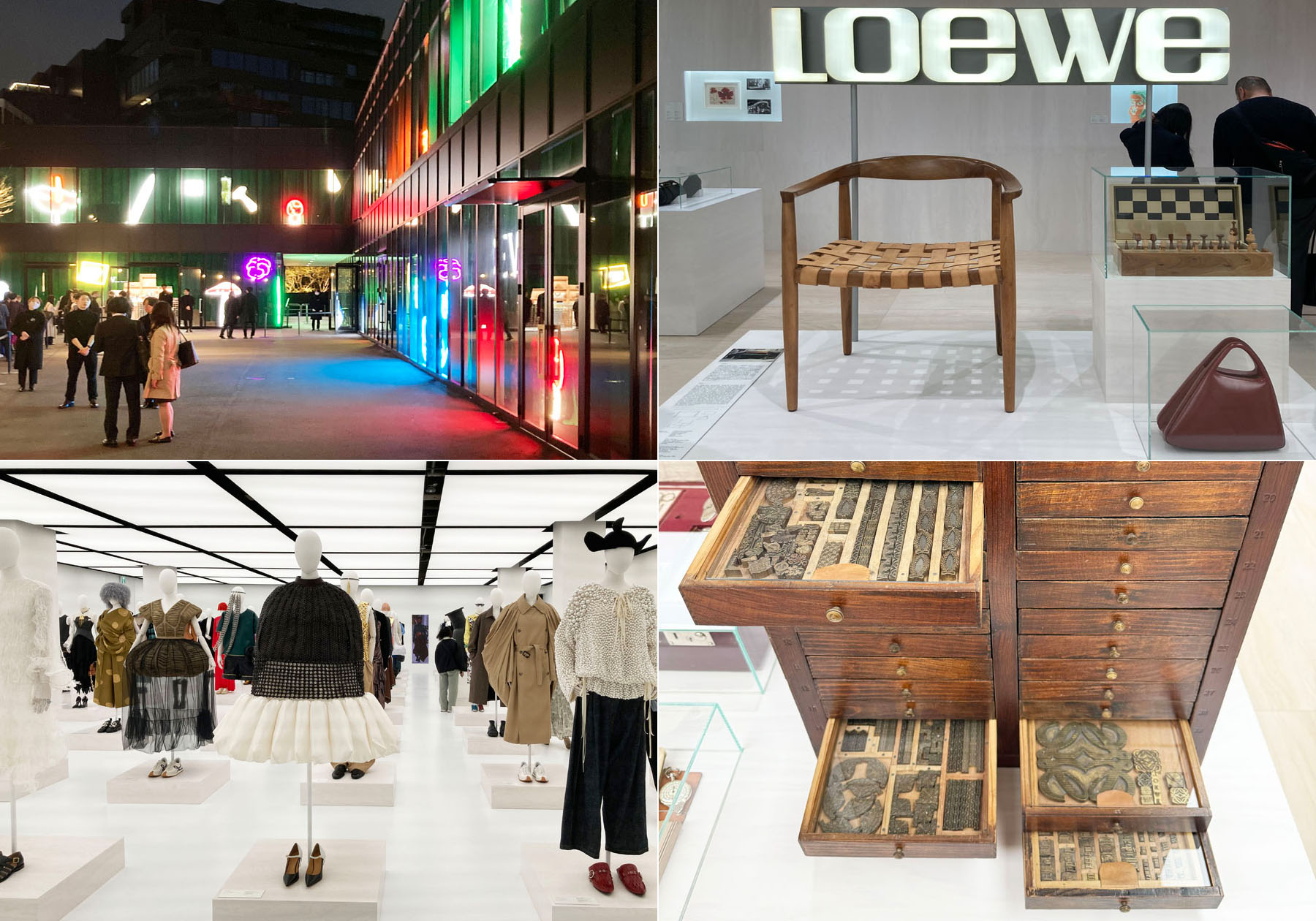
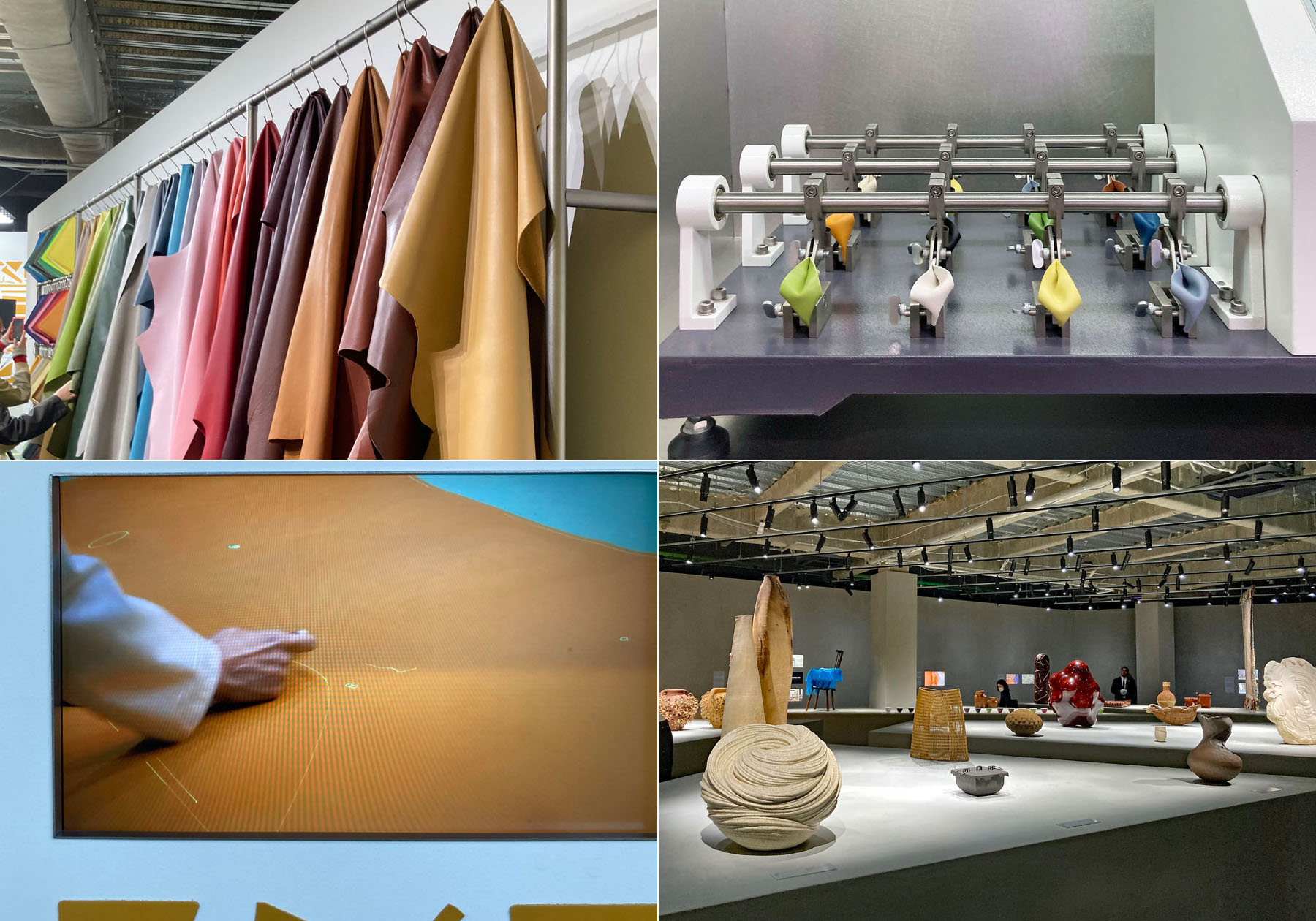
2025.3.27 DESIGN
思わぬ場所で出会うエーディコアの家具
AD CORE DEVISE DESIGN BLOG Vol.155
今年の春はとても不安定な気候で、突然春めいた暖かい日があるかと思えば季節外れの雪が降ったりと、体調管理も大変くらい寒暖差が激しい日が続きました。私もそうですが、花粉症の方は尚更大変だったのではないでしょうか。3月も末になってようやく春らしい気候に落ち着いて関東の桜も一気に咲き始めたようです。卒業や進学をはじめ新しい生活が始まる季節でもありますが、それに伴って旅や移動の季節でもあります。観光旅行や視察目的の旅、仕事のための移動など、旅といっても目的は様々。はじめての街や知らなかった通りなど、初めて訪れる場所は新鮮で楽しいもの。私も仕事を含めていろんなところに移動することがあるのですが、旅先や移動先でエーディコア・ディバイズの家具に思いがけないところで出会うことがあります。
エーディコアは、ブランド発足当時、一般に方が住空間でお使いになる家具ではなく、商業スペースに使っていただく家具、いわゆるコントラクト市場に向けた家具を開発、販売していました。バブル期には、カフェバーブームに乗ったこともありたくさんの飲食店に製品を納めさせていただきました。当時は、行く先々でエーディコアの家具を使用したお店に出会うことがありヒットした製品なんだと実感した記憶があります。バブルが弾けた後は日本の経済が大きく変化していく中で、インテリアや家具のスタイルやニーズも変化していきました。当社の製品は、それまでほぼ100%コントラクトマーケットが納品先でしたが、バブルが弾けて以降、住関連でお使いいただくことも増えていきました。住宅やマンションのモデルルームにたくさん使っていただいたのもこの頃です。その後、インテリアの流行や経済の市場動向も目まぐるしく変化していく中で、エーディコア・ディバイズのデザインテイストも広がり、お使いいただく空間もさらに幅が広がりました。イタリアモダンデザインを意識して生まれたブランド・エーディコアからスタートした製品作りは、クラシックなスタイルをエーディコア流にモダンに昇華したネオ・クラシコ、カタログ撮影で訪れたアメリカ西海岸のインテリアスタイルに影響を受けて生まれたエー・モード、アクリルと木材を組み合わせたPMMA+Woodまで、ブランド展開も広がりました。ブランド数が増え、製品バリエーションの幅が広がったことにより当社の家具を使っていただく空間も広がってきました。商業空間で使っていただくことが多かった当社の製品ですが、現在は病院や老健施設、教育機関などにもたくさん使っていただけるようになりました。シャープでエッジの効いたデザインだけでなく、優しい柔らかな製品が増えてきたのも要因の一つだと思います。
先日訪れた出張先の長崎空港で、保安検査場の前に置かれたスタッキングチェアのFINO(AD-991)に出会いました。意外な場所での出会いはちょっとした驚きもありますが嬉しくもあります。長崎空港の保安検査場は2023年から改修工事が実施され2024年3月に工事が完了しているようなのですが、FINOの使い込まれたその姿からすると、以前に収めさせていただいた製品を引き続きお使いいただいているのだと思います。FINOがデビューしたのが1992年、33年余りが経過していますが未だ使い続けていただいているロングセラー製品です。当社の製品は空港でお使いいただいている製品も多いのですが、先日羽田空港を利用した時には、使い心地と絶妙なサイズ感が人気のネオクラシコ NC-030ラウンジチェアシリーズに出会いました。デューティーフリーのコスメティックコーナーの待合スペースと、免税店事前予約サイトの受け取りラウンジスペースにセットしてありました。どちらも落ち着いた雰囲気を漂わせつつリラックスした空間を演出していました。
街を歩いている時、ふと目に止まった場所にエーディコア・ディバイズの家具を目にすることがあります。出張先でスタッフと食事をするためにたまたま入ったお店に年代物のCERVO(AD-861)が使われていた、なんてこともありました。新しく開発された最新の施設に当社の家具を使っていただくことは、もちろん嬉しくて素晴らしいことですが、思いもよらないところで出会うエーディコア・ディバイズの家具にもなんとも言えない喜びを感じます。最近では私の知人や友人がご自宅でエーディコア・ディバイズの家具を使っていただけるようになりました。ブランドをスタートした時に掲げたコンセプト「21世紀まで作り続けられるデザイン」ですが20世紀を超えてもう四半世紀が経ちました。これからもさらにいろんな場所で永くお使いいただける家具をお届けしたいと思います。(開発 武田伸郎)
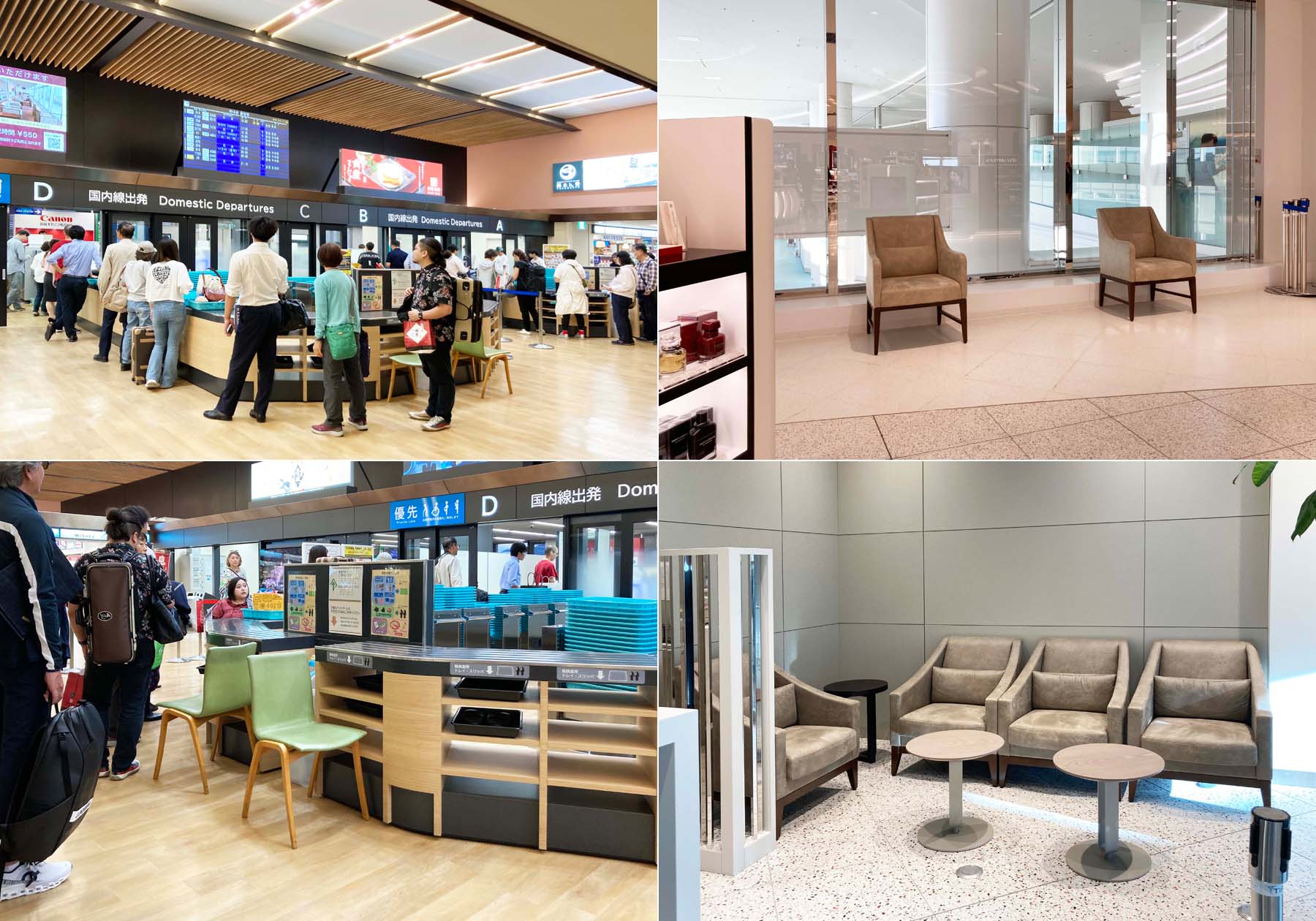
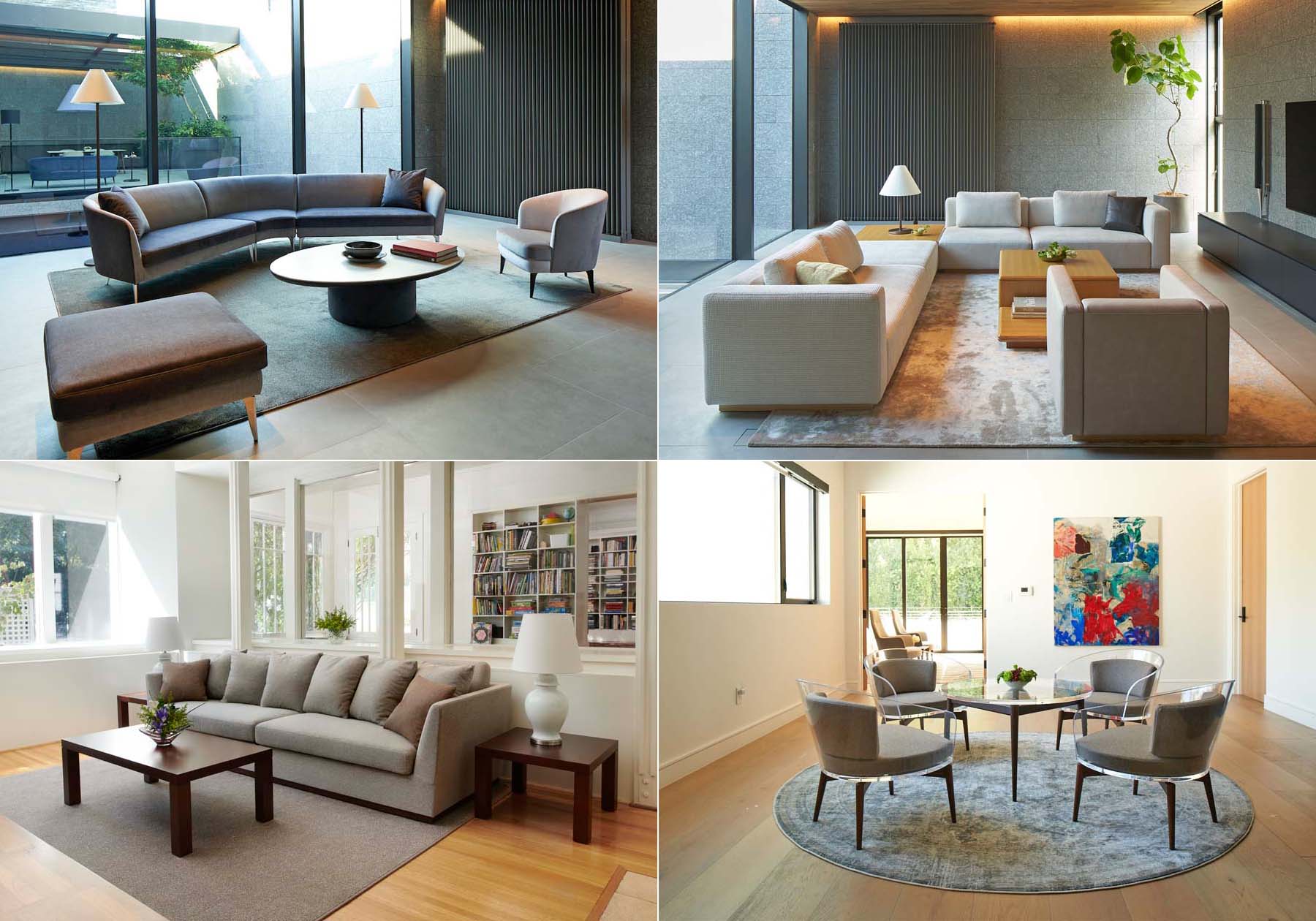
2025.2.27 DESIGN
来日公演大盛況、マルーン5・ジェームズさんお宅訪問記
AD CORE DEVISE DESIGN BLOG Vol.154
2025年2月6日から3日間に渡って、LAのロックバンド「マルーン5」のライブが東京ドームで行われました。2年2ヶ月振りの東京ドーム公演は即刻ソールドアウト、延べ15万人のオーディエンスを魅了する圧巻のライブだったようです。(エーディコア・ディバイズの営業スタッフ・渡邉さんがライブを観覧、感動的なライブで涙したんだとか・・・)このコラムでも度々ご紹介していますが、エーディコア・ディバイズのカタログ撮影を長年にわたってロサンゼルスで行っていました。撮影場所の住宅を決めるために毎回ロケハンで物件を視察するのですが、2013年に視察した建築物件の中に、先日来日公演を行ったマルーン5のギタリスト、ジェームス・バレンタインさんの自宅がありました。
ロックバンド不毛の時代と言われる昨今、2002年のデビューから現在まで世界のミュージックシーンに君臨するマルーン5。アルバム売り上げ枚数は1億枚超え、トップ40のシングルチャートで、グループとして唯一9曲の No 1ヒットを誇るマルーン5。その人気の高さは今回の来日公演でも実証されていますが、世界中で愛される人気の源はロックバンドのカテゴリーにとらわれない幅広い音楽性です。その音楽性を支えているのがギターのジェイムス・バレンタイン。そんな著名なミュージシャンのお宅を、何の前情報もなく、カタログ撮影のロケハンで訪れる機会があったのです。ロケハンの約束の時間にその家に訪問したところご不在のよう。テニスボールが転がっているガレージの側道から、人気のないエントランスに向かいました。ハリウッドエリアのセレブ邸は門やフェンスがしっかりしていてエントランスや中の様子が見えないことが多いのですが、このお宅はすんなり入れたので「こんなんで入れて良いのかな?」と、感じたことを覚えています。そうこうしていると、背中まで届きそうなロングヘアで短パン姿のオーナーと思われる人物が現れ「やぁ遅れてごめん、どうぞどうぞ」って感じで自宅に招き入れてくれました。この方がマルーン5のギタリスト、ジェームス・バレンタインさんでした。
当時彼がお住まいだったのがスチールフレームに水平ラインの屋根、屋外プールが印象的なミッドセンチュリースタイルの住宅。1960年にニール・M・ジョンソンが設計したスチールハウスと呼ばれる住宅でした。室内に入ると、ガラス張りのリビングにはドラムセットとギターをはじめ音楽機材が所狭しと並んでいました。素人ではないことはすぐに分かりましたが「僕はミュージシャンでギタリスト。マルーン5というバンドで日本の武道館でも演奏したことがあるよ」と言うジェームスさんの言葉にも、私をはじめ訪問したスタッフはマルーン5の知識がほとんどなく「マルーン5?聞いたことがあるけど・・・バックバンドのギタリスト?」残念ですが当時はそんな反応しか出来ませんでした。部屋の中のスタンドに掛けてあるギターやケースは貴重なヴィンテージギターばかり。興味津々で眺めていると、ケースから取り出して説明をしてくれたり、目の前でギターを弾いてくれたり、さらには「弾いてみなよ」と、貴重なギターをアンプに繋いでくれたりしました。自分の大切なギターは他人に触れさせたくはないものですが、そんなそぶりも全くなくとても気さくな方でした。ロサンゼルスでカタログ撮影ロケハンでの素敵な思い出です。
部屋を見せていただいている時にジェームスさんから「カタログ撮影の期間は、ツアー中でギターなどの機材は無くなるから撮影は問題ないよ」と言っていただいたのですが、撮影でお借りすることはありませんでした。しかしその後、とある記事でこの住宅と再び巡り合う機会がありました。瀬戸が建築雑誌で見つけたのですが、建築に造詣の深い俳優のブラット・ピットさんが、この住宅を550万ドルで購入したという記事が載っていました。ジェームスさんが2019年に石油王のポール・ゲティの孫であるアイリーン氏へ住宅を売却、その住宅をブラット・ピットが購入したようです。ジェームスさんが購入した当時は90年代風にインテリアが改装されていたそうですが、ジェームスさんがオリジナルの状態に戻したそうです。愛用しているギターもセンスの良いヴィンテージばかりでしたが、インテリアも旧き良きものを知るセンスの持ち主なのでしょうね。お会いした時からさらにセレブリティになったジェームスさん、今はどんな素敵な住宅にお住まいなのでしょうか。興味津々です。(開発 武田伸郎)
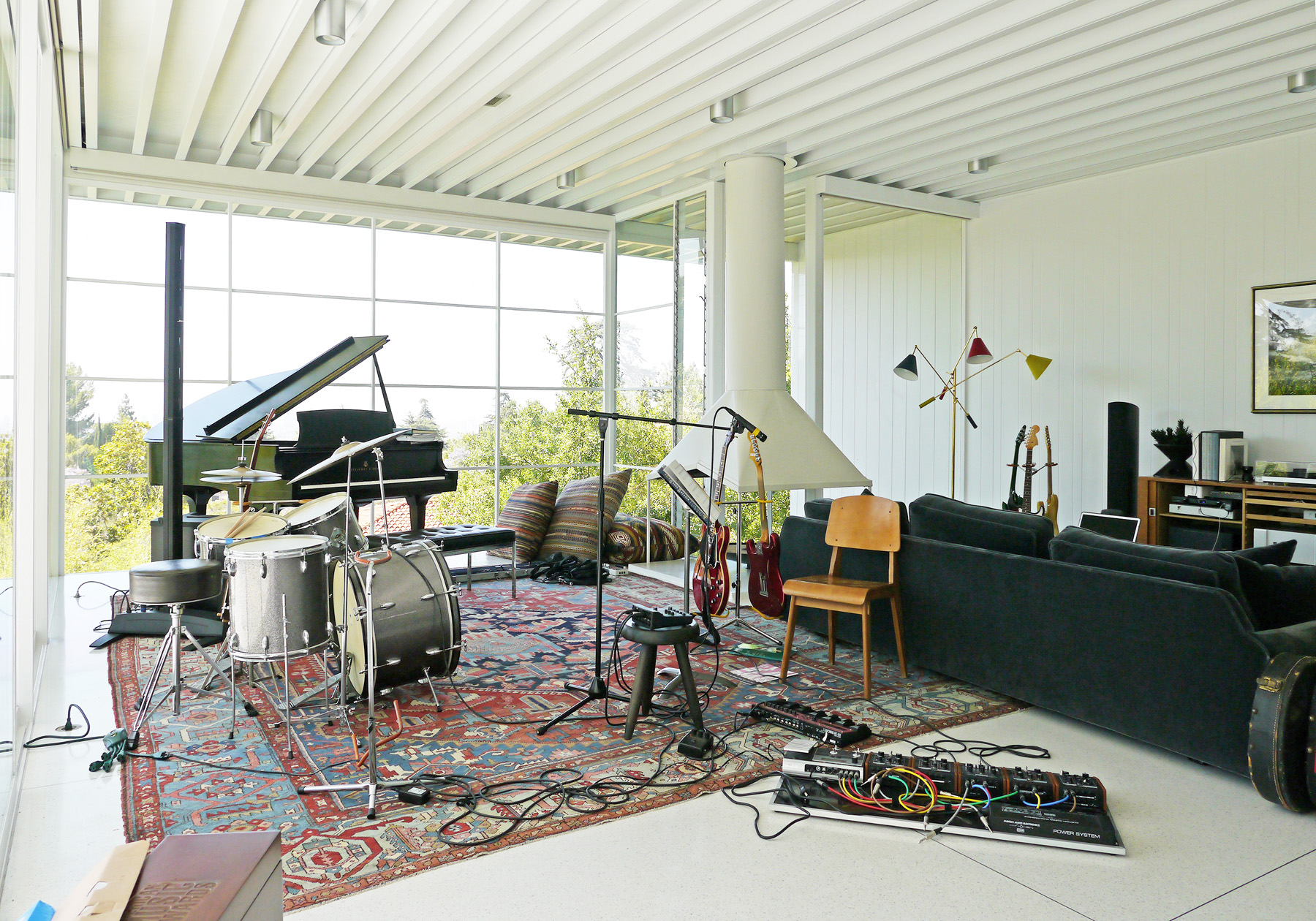
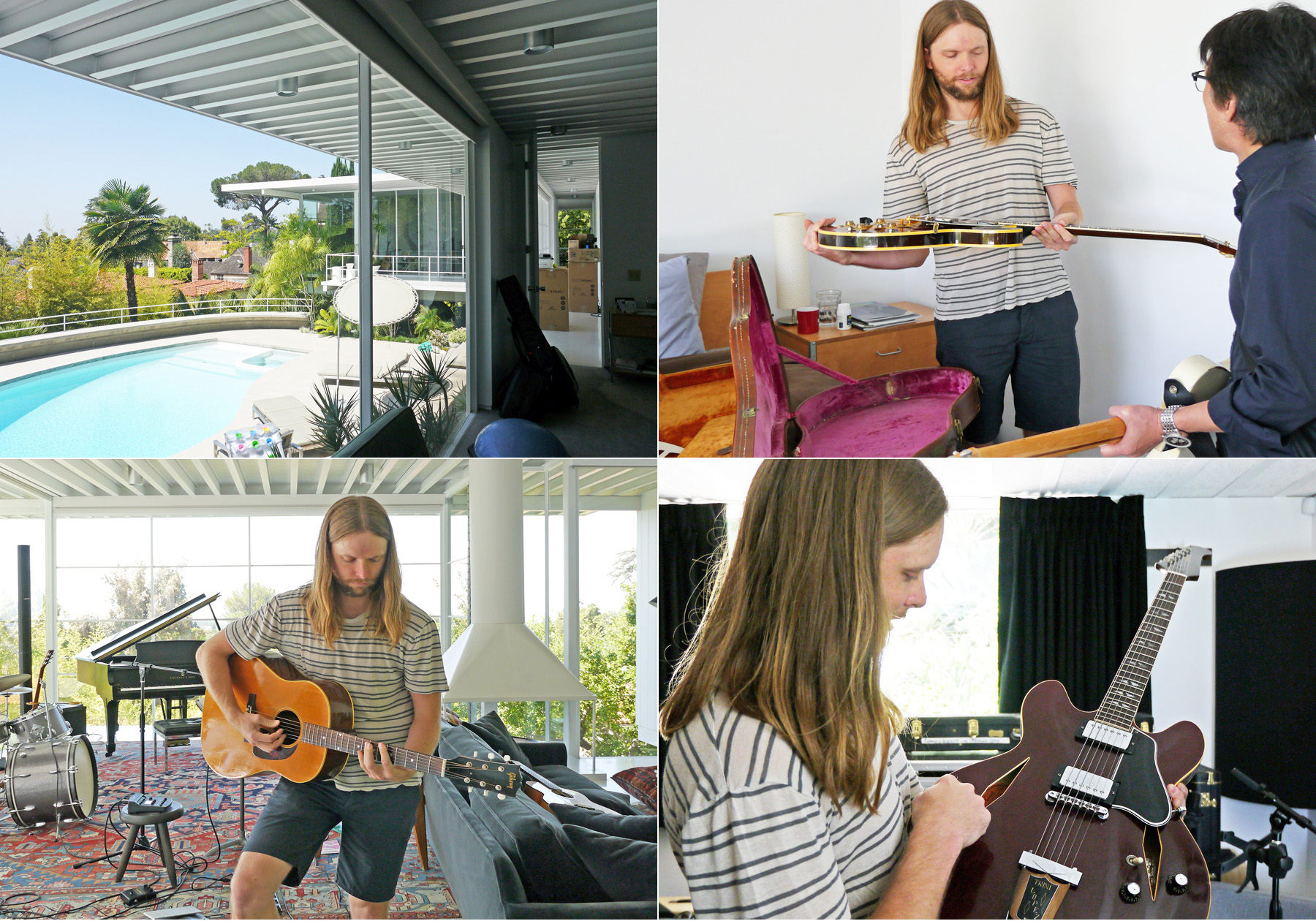